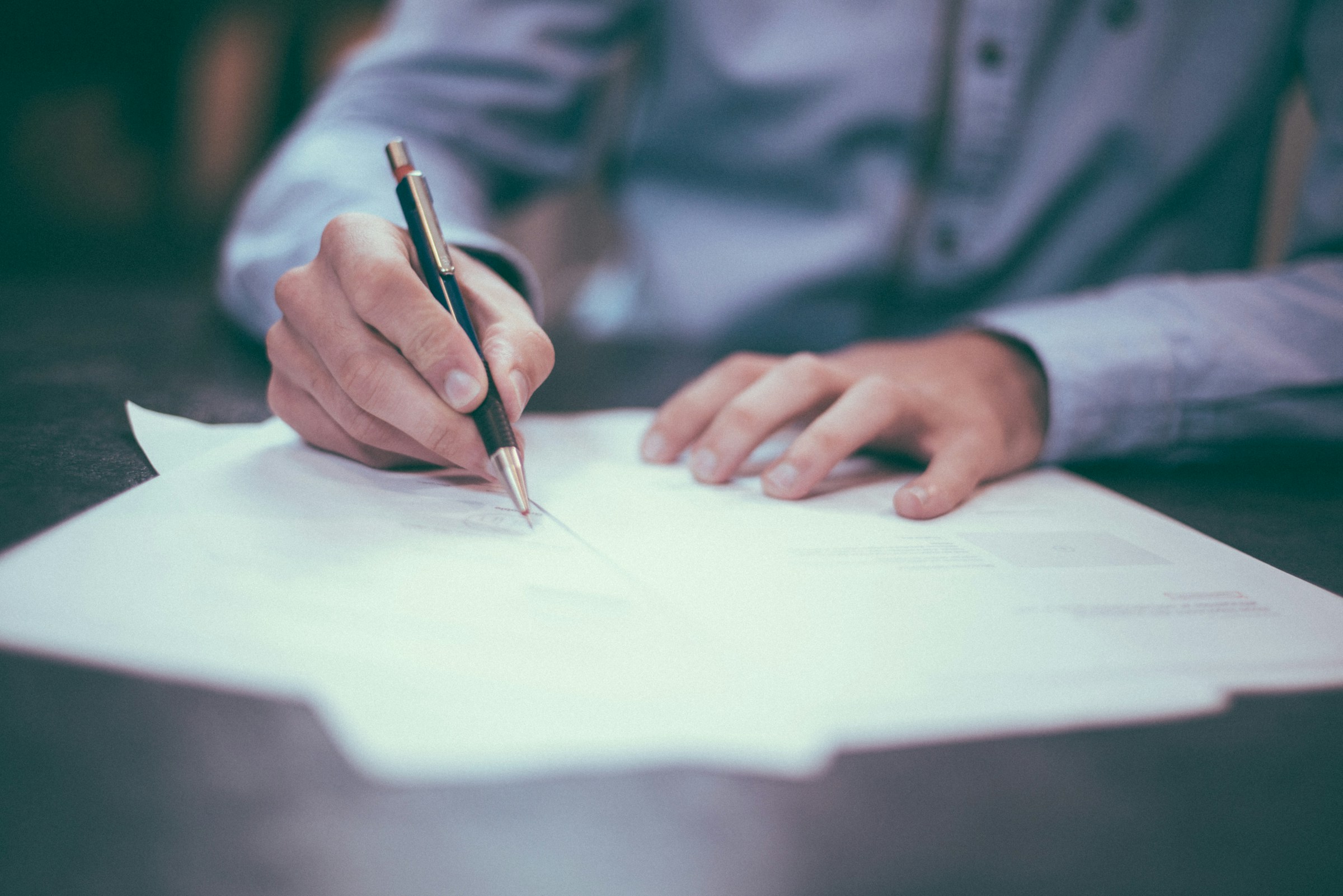
Reliability and Organisation
The organisation of maintenance synthesises and establishes knowledge, which is fundamental for managing maintenance and for running operations. It precedes the implementation of any maintenance management system, given the volume of information to process, the large number of decision parameters to consider and the limited time available to make decisions. Without guaranteeing the organisation of maintenance, the added value of any information system is unlikely to outweigh the costs associated with its implementation. An information system that supports maintenance encompasses the cadastre (the definition of facilities), maintenance plans, information flows and processes for managing interventions and human and material resources. It is implemented on the basis of an analysis of the available information, contextualised by the framework of each organisation. The system generates reliable information, on a routine and continuous basis, which analyses possible actions to improve equipment or operations.
Our clients
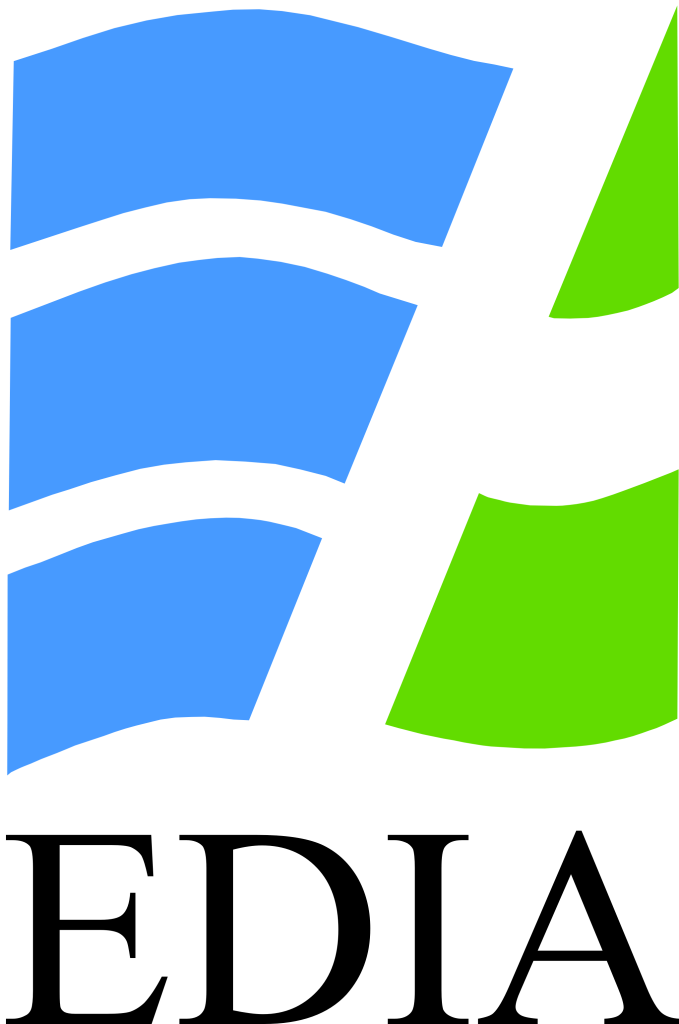
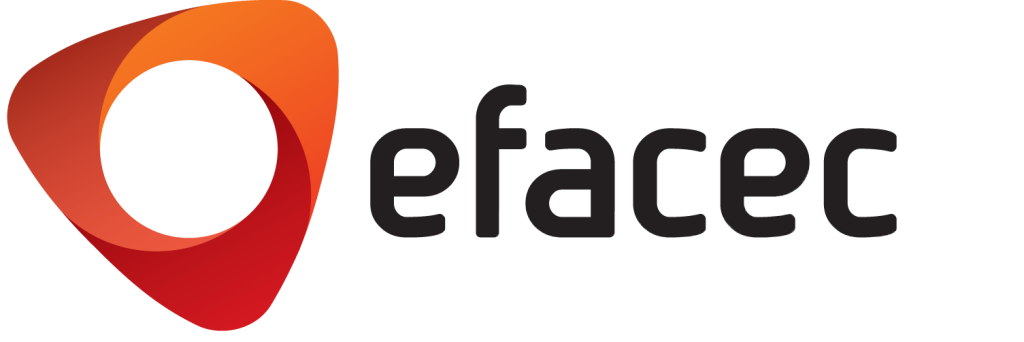
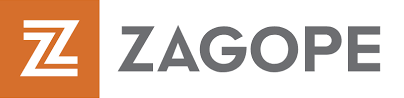
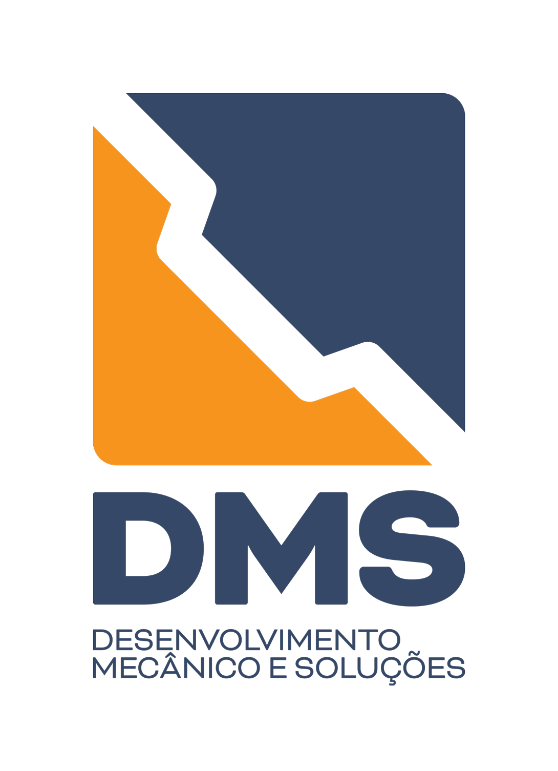
Services
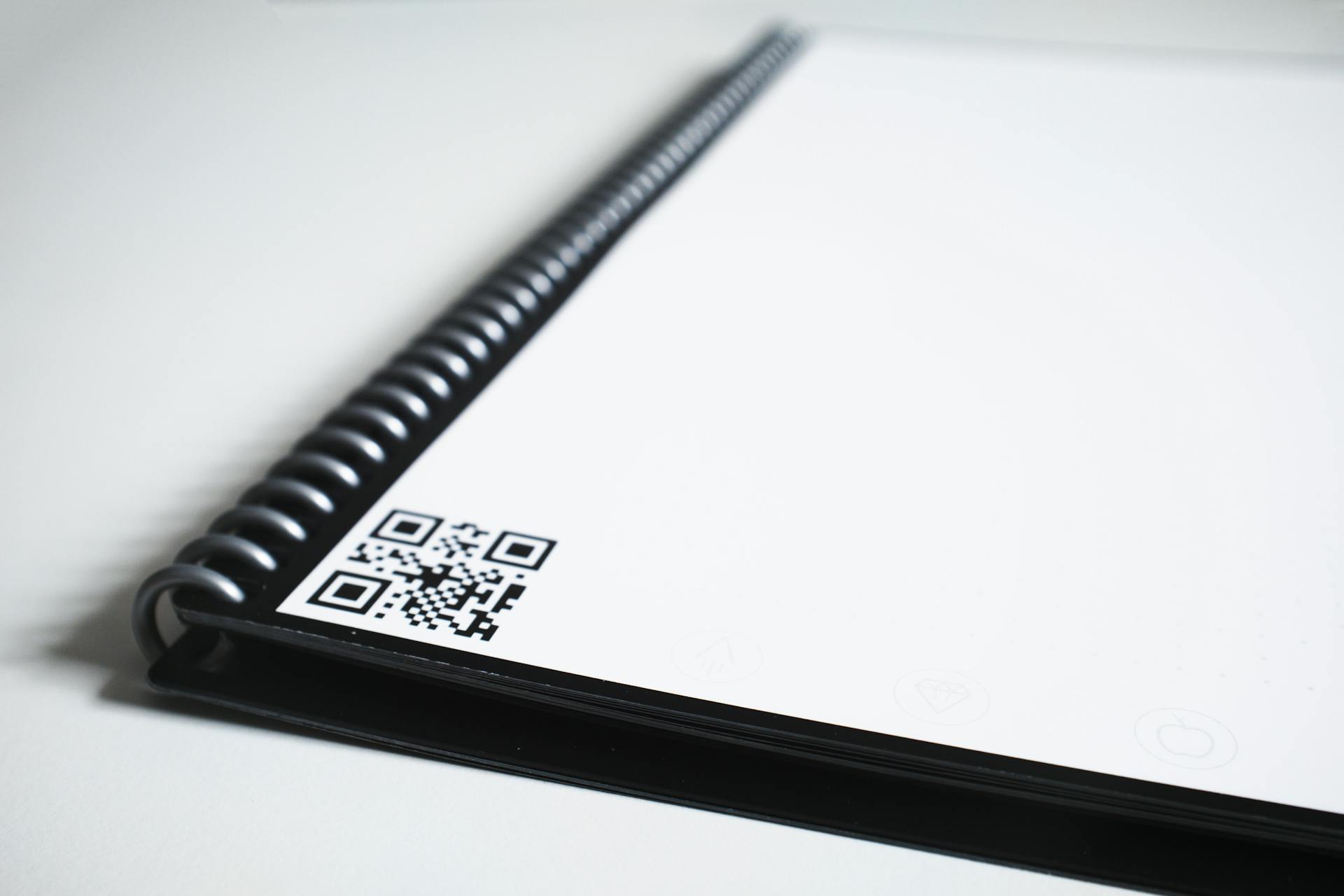
Characterisation of installations and equipment – Registration
Description of layouts and equipment, using a hierarchical and structured description, with technical characteristics, faults, materials, counters and parameters.
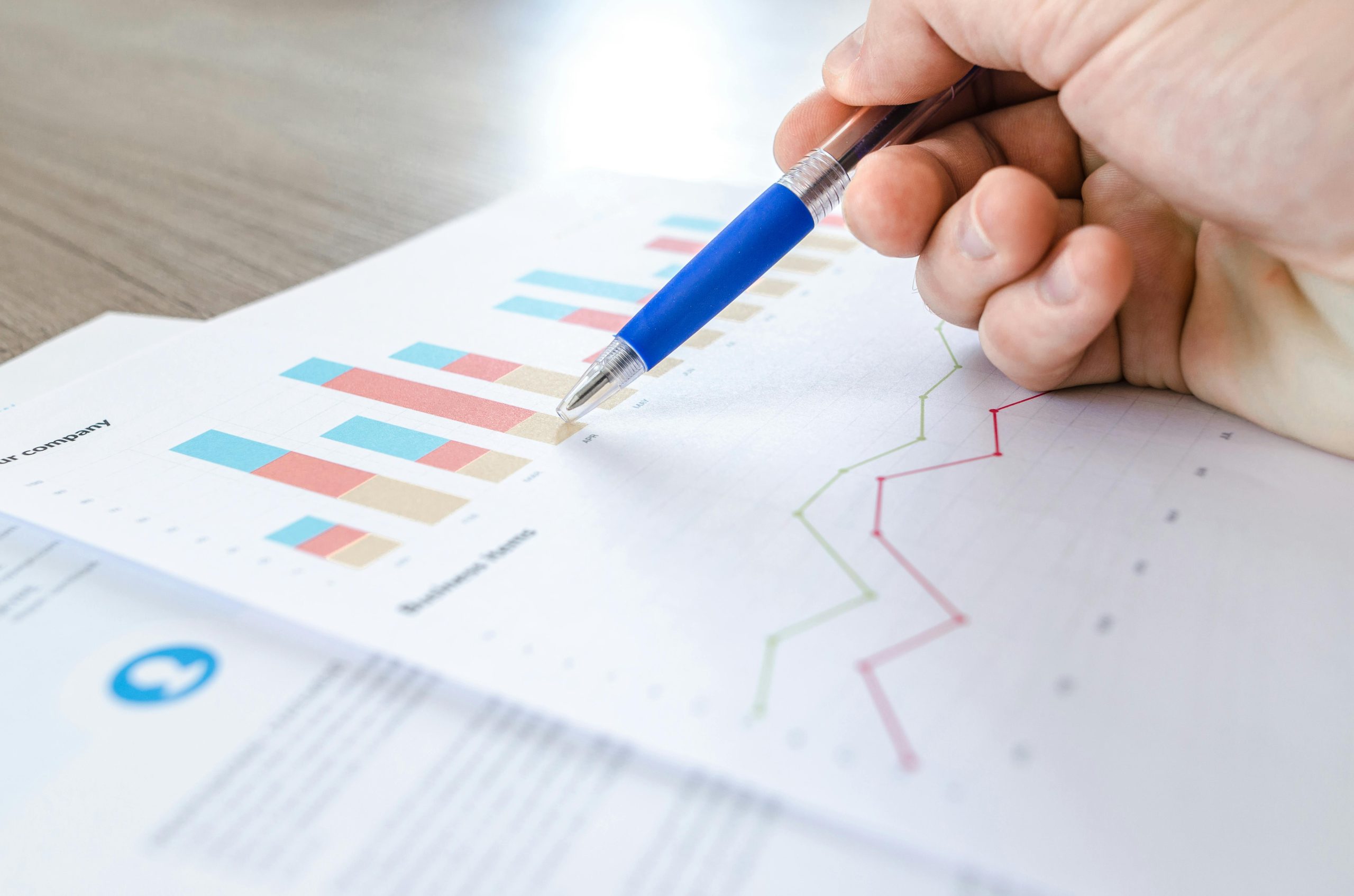
Maintenance and inspection plans
Characterisation of maintenance operations, including maintenance plans or corrective actions, with the associated human resources, services and materials, as well as the resulting planning. Definition of the information flows that support operations management.
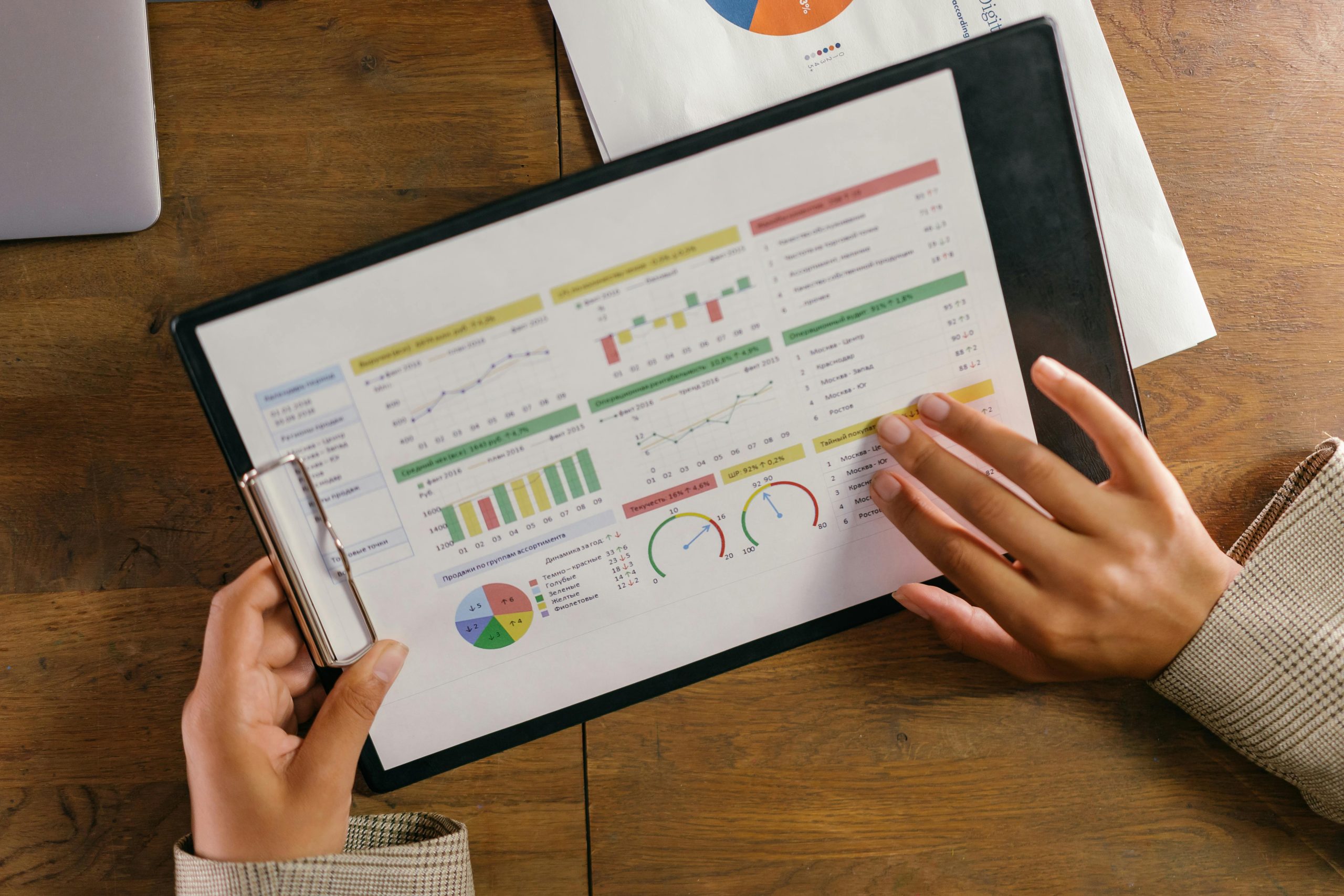
Information flows Metrics and performance indicators
The information is reported in a structured and intrinsically reliable way, allowing information to be generated on a routine and continuous basis that effectively reflects the real situation.
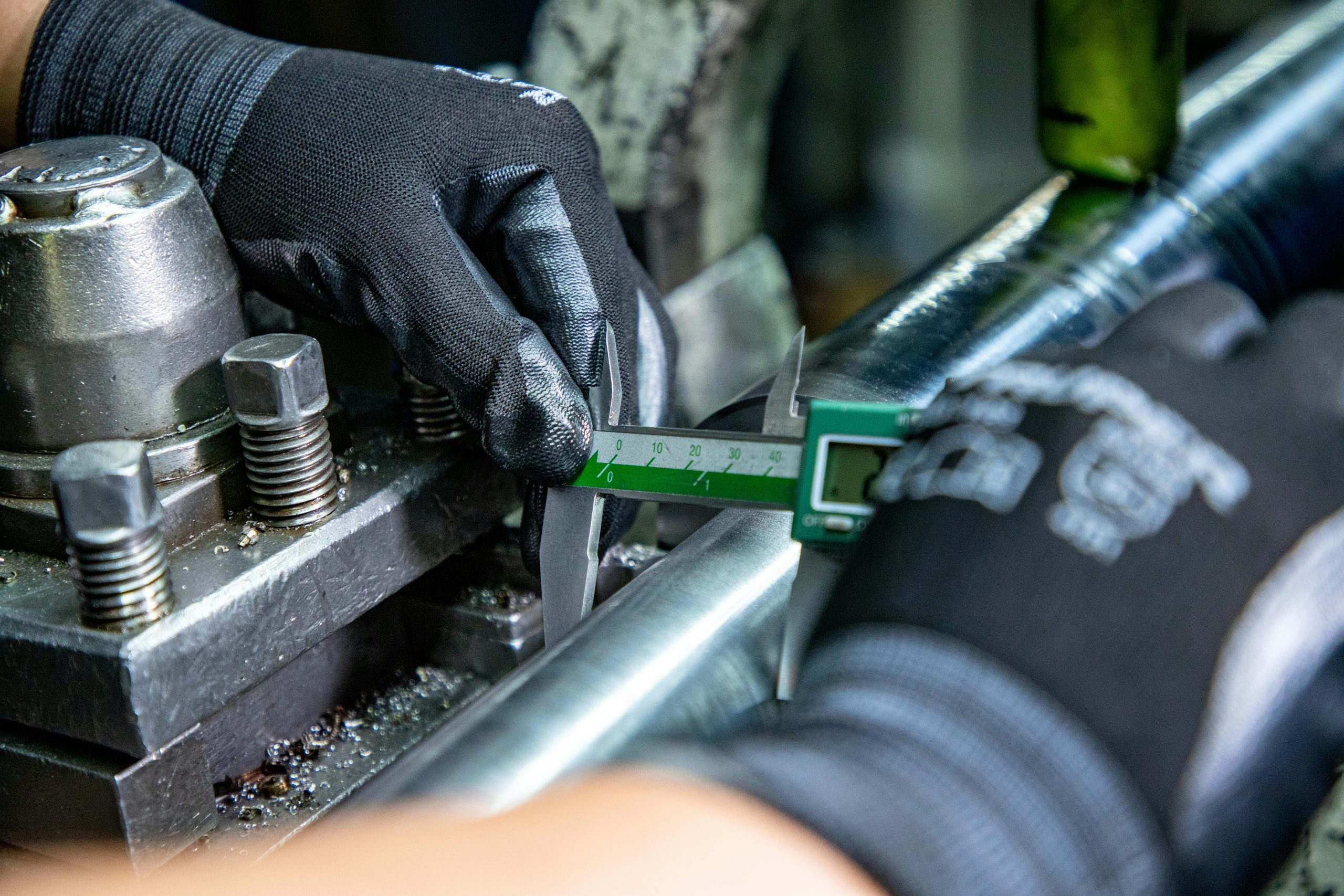
Functional Analysis, Failure Modes and Weaknesses Analysis
Based on equipment architecture, fault analysis, parameter values or counters, actions are devised to overcome weaknesses or adapt productive or operational capacities to processes or production or improve efficiency.
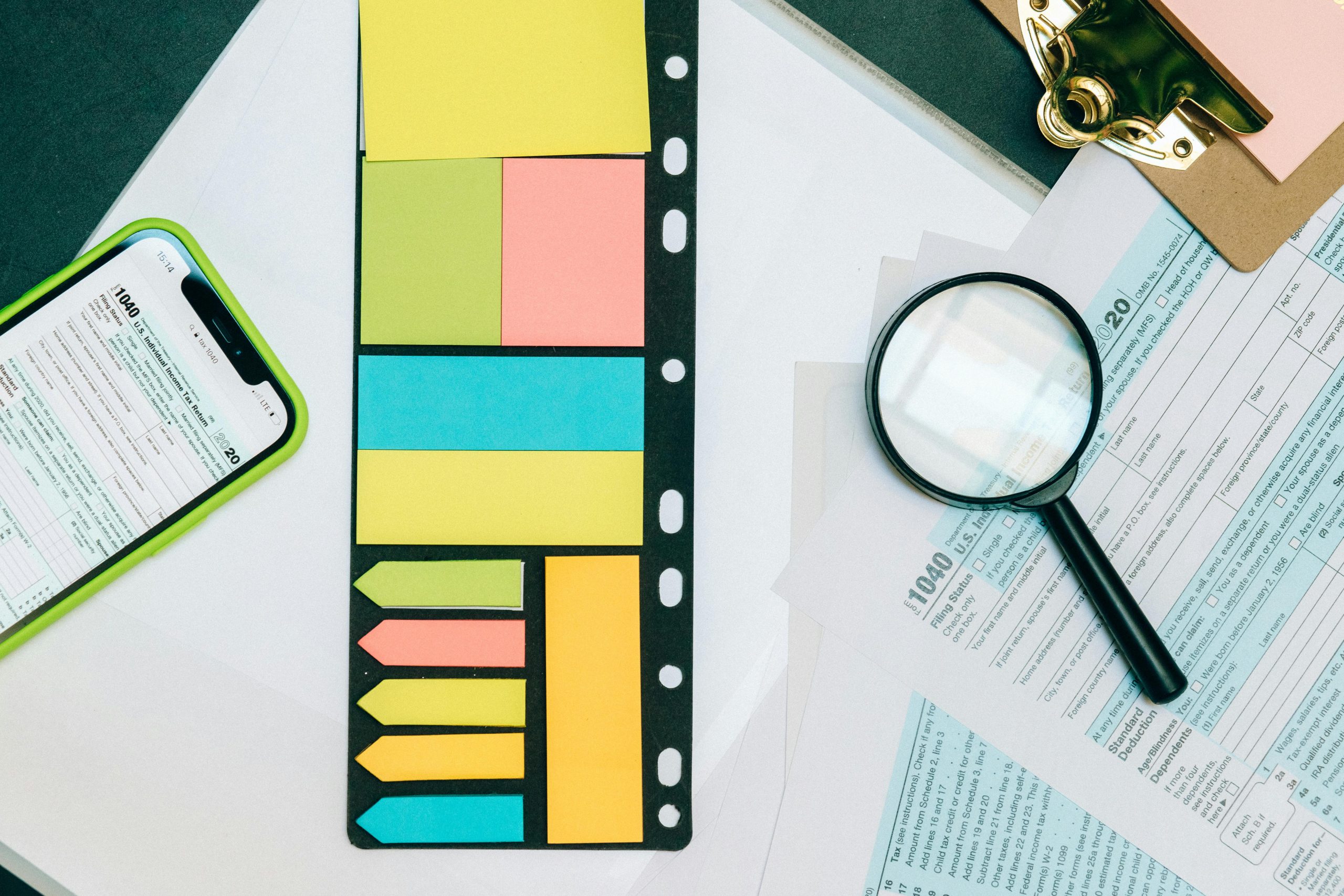
Auditing
The audits provide a contextualised image to situate each company in its sector and grade its organisation on scales of efficiency and operability.
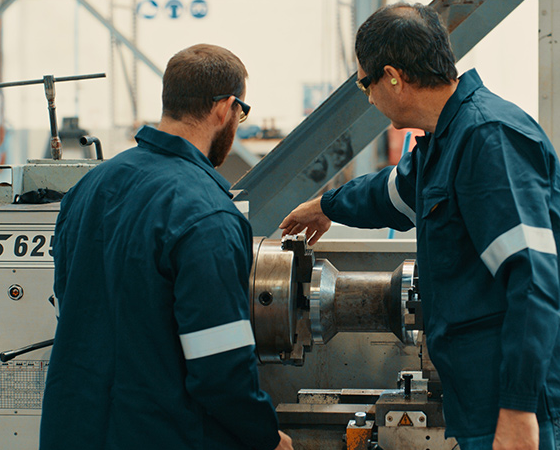
Specialised Maintenance Training
Knowledge transfer in areas of advanced specialisation and ‘know-how’ based on the analysis of practical cases.
Methodologies
Project Review from a Maintenance Perspective
Analysis of construction solutions in relation to operation and maintenance, following a joint approach of operation – maintenance – quality – investment, which allows us to have, from the initial phase, a perception of global needs throughout the life cycle, translated into the quantification of operations, costs and risks.
Applying the RCM Methodology
Analysis of a system in terms of maintainability, with a view to defining the appropriate operations to avoid or minimise failures
Applying the RAMS Methodology
Analysing a system from the design phase to the operation phase using the RAMS methodology, in order to confirm and justify compliance with the defined RAMS requirements.